Case Study: Media supply for sterile steam generation
The topic of sterile processing in AEMPs in clinics and hospitals represents an essential element in ensuring proper operation, the protection of the instruments used and the associated patient safety.
This is especially true for service centers whose business model and success lies in the reprocessing of sterile supplies.
Due to identified increased repair and repair replacement costs, the experts at Gebrüder Heyl Vertriebsgesellschaft were commissioned to conduct a process analysis in the AEMP department in February 2020.
Based on a qualified process analysis, which included, among other things, the procedural recording of the existing water treatment plant, operated equipment technology, selective evaluation of the instrument inventory and all other service aspects located at the site, including logistical processes, the results were presented to all departments involved. Particular attention was paid to the area of water analysis. In addition to brief chemical analyses during ongoing operations, supplementary samples were taken and subsequently analyzed by an accredited laboratory.
The expert evaluation of all data revealed a need for action in the following areas:
- the process water plant technology,
- the media-carrying piping systems, and
- in the subsequently used equipment technology,
which were identified within the AEMP department as possible causes for the significant increase in repair and repair replacement costs in the instrument area.
Due to the complex interplay of all factors in the instrument reprocessing chain, Gebrüder Heyl Vertriebsgesellschaft was then commissioned in an advisory capacity with:
- the project planning & consulting,
- the subsequent implementation of the recommendations for action as well as
- the continuous validation of the measures introduced.
commissioned.
The implementation period for all the individual points shown in the project plan, which are successively coordinated in their logic, was set at approx. 3 years.
In the first project phase, December 2021/January 2022, the process water plant technology was extended by an additional reverse osmosis with EDI. At the same time, the existing on-site blending bed was optimized with regard to its inflow for the now redundant plant operation. This was accompanied by the integration of qualified online monitoring of water hardness by means of Testomat® 808 and a multi-stage monitoring concept for silicates based on the Testomat® 808 SiO2 device design. Here, silicate monitoring takes place on each line in the first step downstream of the EDI and additionally as the last monitoring point downstream of the first mixed bed filter.
In order to ensure the continuous processing of the highly sensitive sterile material, a bridging concept was already developed during the planning of the conversion measures, so that all conversion measures could be implemented during ongoing operation.
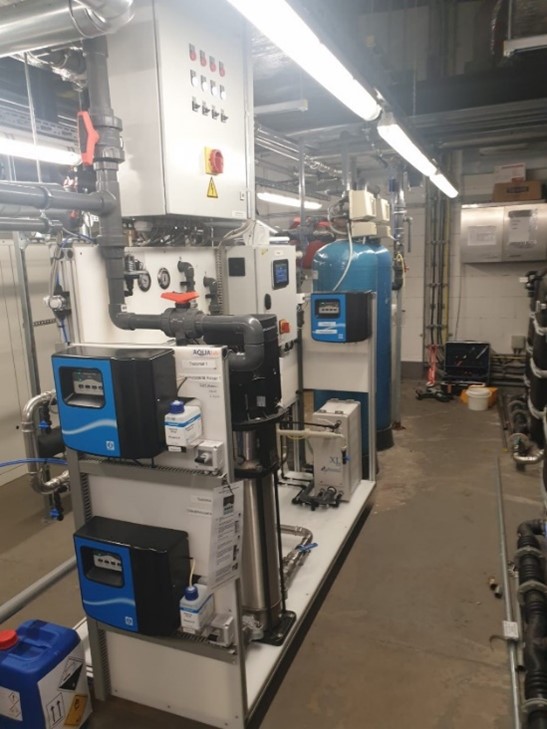
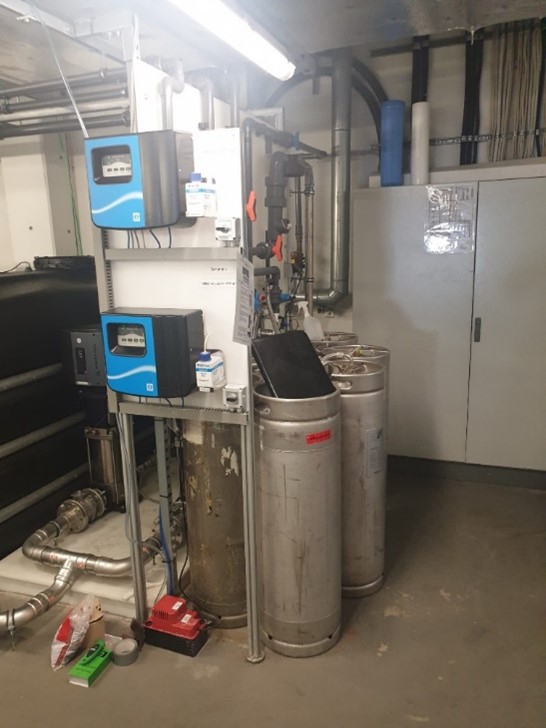
The media analysis showed a conductivity of 0.068 µS/cm and a silicate content of 0.058 mg/l.
The soft water tanks were cleaned and disinfected in parallel because they were a source of process water contamination.
As a result of introduced contaminants, media-carrying pipelines had to be inspected endoscopically and visually with regard to the technical design of the transitions for surface changes and in some cases renewed.
Steam sterilizers were inspected and chamber separation and chamber renovation were carried out. In addition, new clean steam generators were commissioned to supply steam to the sterilizers.
It is not only the issue of water that requires continuous attention within the overall process. The media monitoring of the pure steam generated also has to be subjected to a permanent quality check. For this purpose, a sampling point with a cooler was integrated for regular condensate sampling.
Measurement samples were taken in all steam sterilizers, and the data collected and validated. The analysis revealed conductivity values between 1.0 - 3.0 µS/cm and silicate values of less than 0.1 mg/l. The values were reliably below not only the limit values of DIN EN 285, but also the recommended limit values of the Working Group Instrument Reprocessing (AKI).
Result: All the optimization measures implemented have had a demonstrably sustainable positive effect on the media quality (water & steam) and the project objectives have been achieved.
Once the media supply was at the best level, the optimization of the WD units was carried out. By extending the program steps of the cleaning and conditioning programs, it was possible, for example, to improve the surface passivation of the instrument sets by using citric acid.
During the project, there was a continuous exchange with all specialist departments, in particular the AEMP management, the hygiene officers, the building services department and the experts from Gebr. Due to the complexity of the topics, targeted training measures were carried out. An essential component of these was, among other things, the monitoring of the individual measures by employees of the specialist departments concerned. At each point in time, the interaction of the measures was evaluated and monitored by means of analyses.
The regular on-site analysis by AEMP staff will continue in the future with the PPM 150 hand-held photometer.
The sensitization of employees to the topic of "surface changes on and on instrumentation" will be supported by an in-house workshop in the 2nd quarter of 2022.
The extensive spatial division of the AEMP and the strict separation of the "unclean and clean side" make it obvious to enable the visualization of the media and system status of the water treatment and instrumentation. During the development of the new plant concept for the water treatment, attention was paid to the fact that the monitoring technology used is suitable for ensuring data transfer to higher-level systems.
With the multi-parameter control concept of the NeoTecMaster®, the data transfer and the visualization at the site are implemented in the network by means of an Ethernet interface.
Today, the current media and system status can be monitored from any PC workstation in the facility (limit values for water hardness, monitoring points for silicates). At present, 5 parameters are continuously monitored. In the future, the modular design of the NeoTecMaster® will allow the integration of further measurement technology and the retrofitting of further control contacts at any time in the case of plant expansions.
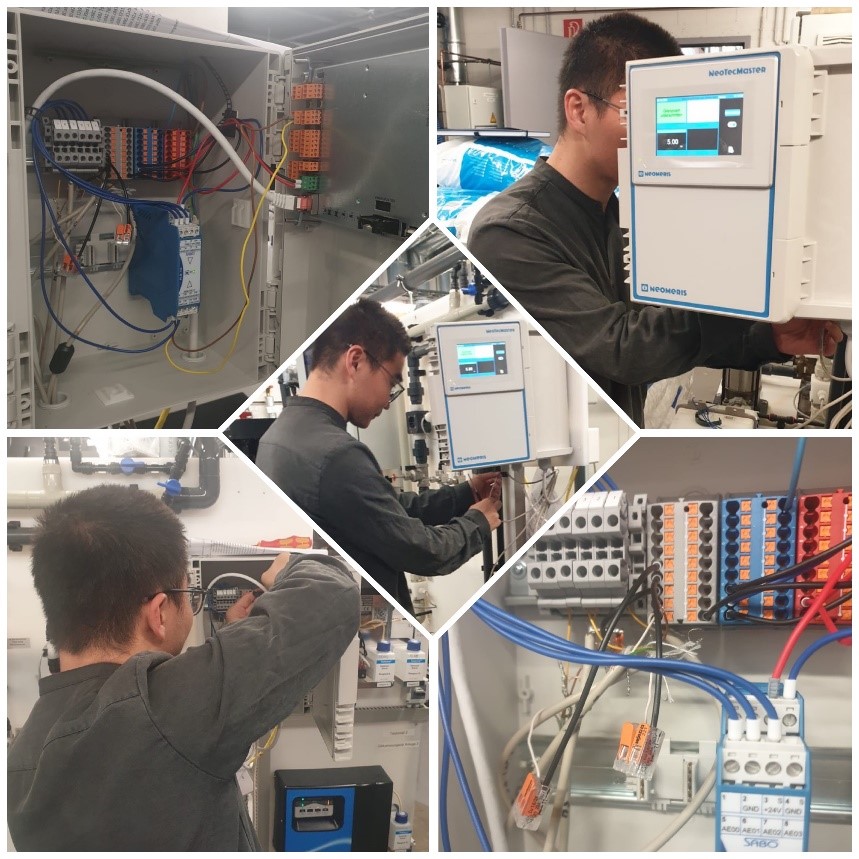
The deficiencies in the process water plant technology, the piping systems and the equipment technology identified during the process analysis have been eliminated. The media quality consistently meets the limit values, which must be well below the specifications of DIN EN 285.
A reduction in repair and repair replacement costs in the instrumentation area and a minimization of the maintenance effort for the instrumentation used can also be noted.
The instruments show a reduction in surface corrosion and silicate deposits. This ensures greater patient safety.
Conclusion: Small cause - big effect. The risk has been sustainably reduced by the measures taken.
Detailed information on this can be found in our Business Case Sterile Processing - Safety in AEMP.
Sterile processing | Optimization of the clinic AEMP - Neomeris: industrial water treatment
June 2022